
Precision Maintenance
Laser Alignment
Laser Alignment
Nearly 50% of machine failures are due to misalignment. Indications of misalignment in rotating machinery are shaft wobbling, excessive vibration (in radial and axial directions), excessive bearing temperature (even if adequate lubrication is present), noise, bearing wear, and coupling wear. Misalignment can be especially detrimental to rolling-element bearing life.
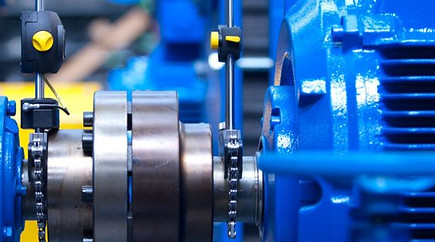
Machines which are precision aligned will function for a longer period and costs less to run. Common misalignments are the result of two rotating shafts not parallel to one another, either by a slightly offset or angled gap at the coupling. However, many times it is both, which is called a compound misalignment.
There are several causes for misalignment including:
-
Pipe strain
-
Thermal expansion
-
Human error
-
Wear causing sheave to deform
-
Baseplate settles irregular to form a soft foot
-
Inaccurate assembly of components, such as motors and pumps
The primary point to remember is that any unsteady motion or movement to shaft center lines that goes against the intended motion of the machine can cause bearing or couplings to be stressed and the seals to fail. In addition to shaft alignment, we also offer belt and chain alignment.


American MTS has the equipment and expertise to provide an extremely accurate alignment. Utilizing state of the art laser alignment equipment optionally enhanced with motion amplification technology we can help you maximize equipment reliability and reduce energy costs.
Onsite Balancing
Onsite Balancing
Lorem ipsum dolor sit amet, consectetur adipiscing elit, sed do eiusmod tempor incididunt ut labore et dolore magna aliqua. Ut enim ad minim veniam, quis nostrud exercitation ullamco laboris nisi ut aliquip ex ea commodo consequat. Duis aute irure dolor in reprehenderit in voluptate velit esse cillum dolore eu fugiat nulla pariatur. Excepteur sint occaecat cupidatat non proident, sunt in culpa qui officia deserunt mollit anim id est laborum.
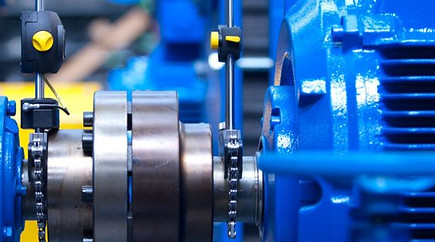
Lorem ipsum dolor sit amet, consectetur adipiscing elit, sed do eiusmod tempor incididunt ut labore et dolore magna aliqua. Ut enim ad minim veniam, quis nostrud exercitation ullamco laboris nisi ut aliquip ex ea commodo consequat.
Ultrasonic Lubrication
Ultrasonic Lubrication
As part of our commitment to your plant’s reliability, American MTS has invested in technology that allows us to determine when a bearing needs grease and then adds the exact amount needed avoiding over or under greasing. This technique utilizes ultrasonic technology. Ultrasound is the first detectable metric to signal bearing wear and even lubrication needed.

Taking measurements with an ultrasound device is the best, and easiest way to determine when your bearings require grease. Observing changes in dB’s is the first sign that your bearing requires lubrication. This provides superior performance to time or run time based methods as you only lubricate when needed.
Since most re-greaseable bearings are in closed housings, the only way to know when a bearing is first in need of lubrication is monitoring with an ultrasound device. Over time, bearing grease degrades and friction levels increase which is detectable with ultrasound. Ultrasonic lubrication allows users to carefully monitor a bearing while adding grease. As grease is added to the bearing the decibel levels will decrease. Once dB levels begin to climb slightly, you know you have reached the optimal level of grease.

Storage Programs
Storage Programs
Keeping operations running with minimal downtime means stocking some spare machine parts. In the case of electric motors, attention is required to make sure they are ready to go when needed. An ideal storage location is climate controlled with minimal or no vibration and rodent free. In addition regular maintenance needs to be performed. This helps keep the internal areas properly lubricated and the winding dry.



Shaft Rotation
This should be done at least quarterly to redistribute the bearing grease. American MTS provides free stickers to place on the ends of shafts with a clock face. Once spun a few rotations, the position of the shaft is left 5 hours ahead of where it was. American MTS will gladly help you in setting up your own in house program or provide this service for you complete with emailed reports.
Insulation Testing
Motor manufacturers and EASA recommend periodic insulation testing. This is especially important if motors are stored in conditions above 60% humidity as the insulation will absorb moisture. Winding heaters or trickle heating can also be used if storage area humidity is above 60%.

Offsite Storage Programs
American MTS offers managed spare services at any of our locations or nearby your plant. This service includes : ​
​
-
Motors fully tested before storage
-
Vibration free warehouse space
-
Climate controlled below 60% humidity
-
Clean, dry rodent free environment
-
Monthly shaft rotation
-
Monthly insulation testing
-
Free delivery between 7:00 AM - 5:00 PM
-
24/7 after hours delivery available
